How sand becomes glass
Share this blog:
Most of us know that glass is made from sand. But how, exactly? Learn all about it in our quick guide.
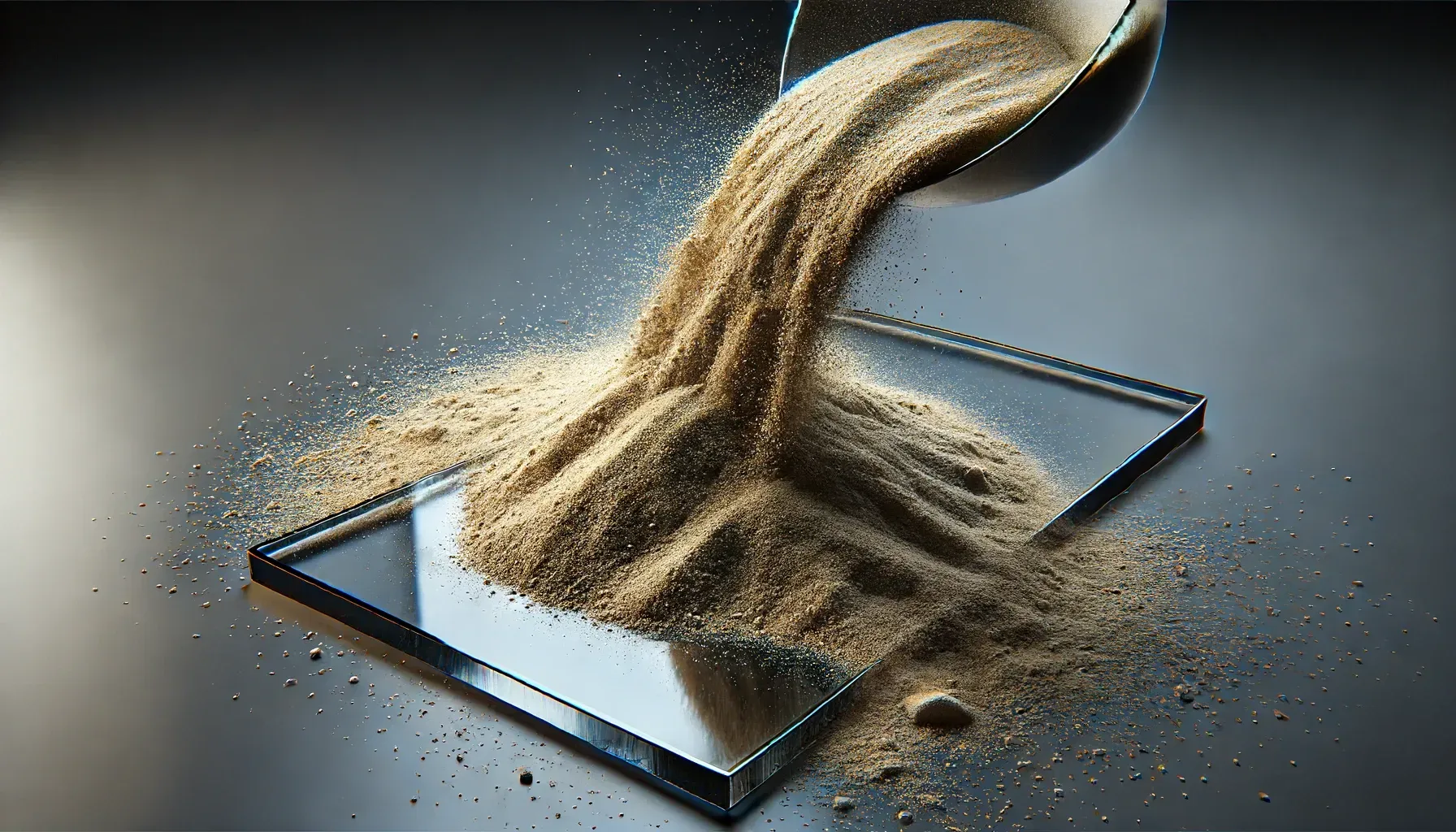
Visit the desert near Alamogordo, New Mexico, and you might come across a green glassy substance known as trinitite.
Trinitite is the residue left after the US tested the Trinity nuclear bomb in July 1945. The heat was so intense that the sand turned into glass.
This example from history illustrates a basic point about the production of glass: sand plus heat equals glass. But to make commercial glass, you need to add more ingredients – and you can do it without a nuclear blast (thankfully).
How hot is hot?
If you've walked on a beach on a hot summer's day, you'll know that sand can get pretty toasty. But a summer scorcher will never be enough to melt sand – the first step in turning it into glass.
No, to melt sand you need extreme heat: around 1,700°C (3,092°F). That's the temperature of a
spacecraft returning to Earth.
Let's put it this way – you're going to need a bigger oven that your kitchen can provide if you want to make glass.
Why does sand become glass?
There are two stages to the transformation of sand into glass: extreme heat and then rapid cooling.
Sand has a crystalline structure. It's composed of minuscule quartz crystals that are in turn made up of silicon dioxide (or "silica") molecules.
Extreme heat affects these molecules. When sand melts, it loses this crystalline structure and gains a new one – somewhere between a liquid and solid state.
You may have heard people say that glass is a liquid. This is based on an old misconception about the manufacture of windows.
It is true, however, that before it sets, glass exists in a sort of molecular limbo – an in-between state that scientists call an "amorphous solid".
What is sand mixed with to make glass?
You can make glass simply by heating and then rapidly cooling sand. But commercial manufacturers add some special ingredients.
Take one vat of sand. Add waste glass from recycling. Stir in some soda ash (sodium carbonate) and a dash of limestone (calcium carbonate). Prepare on a high heat and
voila! You have glass that's ready for market.
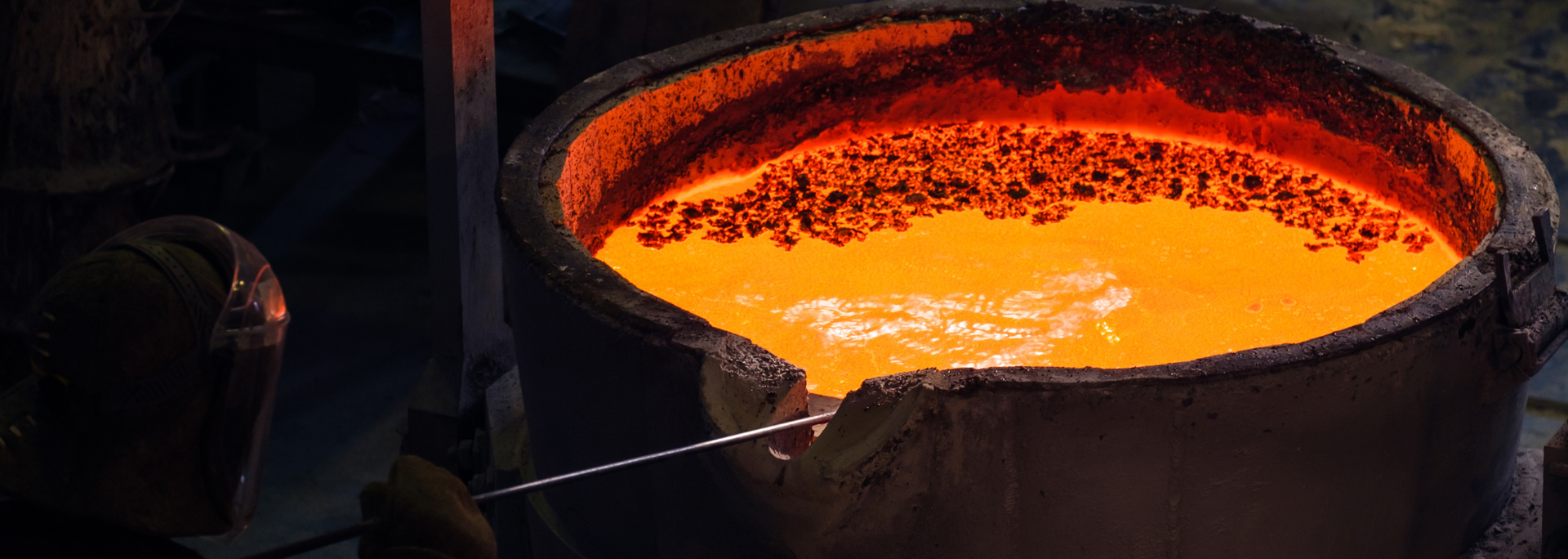
Some manufacturers will add colourants and refining agents. But whoever's in charge of the process, the essential ingredients are sand, soda ash and limestone.
The soda ash serves the important purpose of lowering the sand's melting point. Why? Because extreme heat is extremely expensive – and wasteful. By reducing the melting point, manufacturers can make glass in a more energy-efficient way.
However, this creates a problem. The lower melting point means that the sand could dissolve on contact with water. The limestone is a stabiliser that's mixed in to counteract this.
How is glass shaped?
Once the sand is melted, you can set it in different ways. If you want to make a bottle or other receptacle, for instance, you can pour the liquid glass into a mould and cool it rapidly.
Or if you want to create a flat panel for a window, you float it. This involves feeding the molten glass into a tin bath.
If you're imagining a bath made out of tin, think again. This is a bath that's filled with molten tin. Molten tin is denser than glass, allowing the molten glass to float on the surface.
Afloat on a sea of molten tin, the glass forms a perfectly smooth ribbon. The temperature is slowly rolled off until the glass can be lifted out of the bath.
As well as moulds and tin baths, there's good old-fashioned glassblowing – a process that's barely changed since the first century BC. It's incredible to think that Venetian glass sculptures, say, were made with nothing more than glass and human breath.
Can you make glass without sand?
At the University of Cincinnati, Carlos Co and his colleagues made a fascinating
discovery. They managed to make a kind of glass out of just sugar, oil and a surfactant – no sand needed.
The mixture was shaken up, heated to 250 degrees and then cooled. The result is a kind of emulsion – but because it contains sugar, not water, it's hard like candy rather than gloopy like mayonnaise.
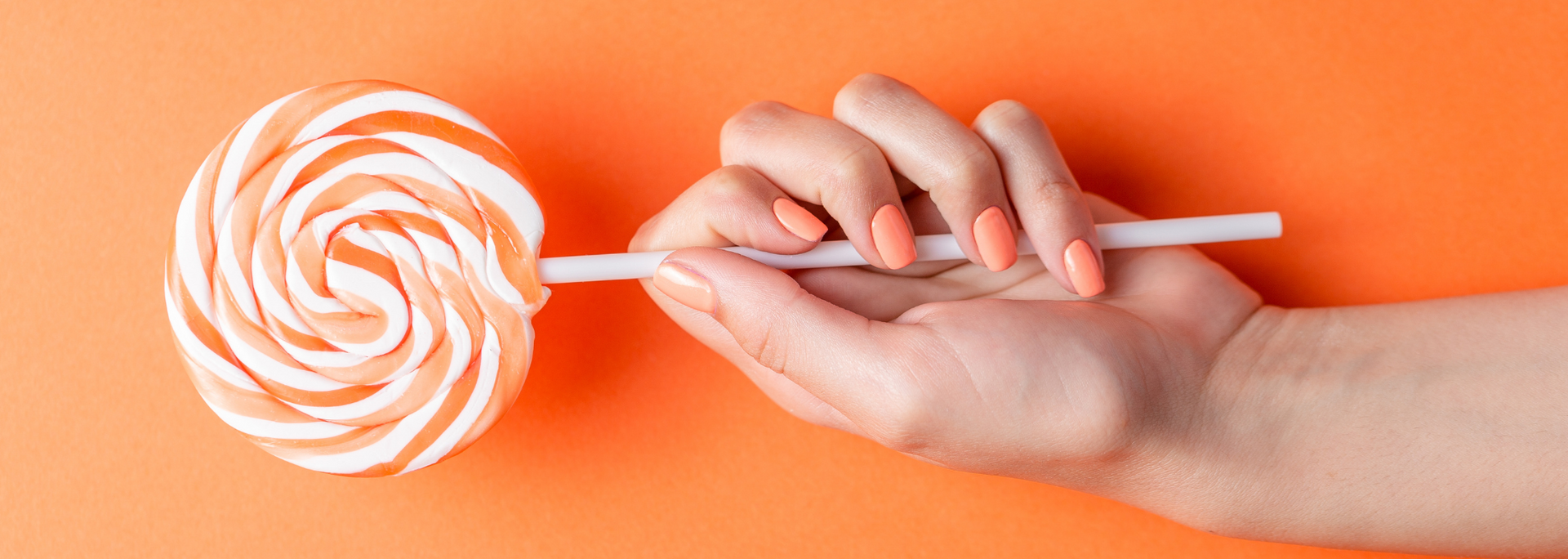
Co and Co. believe it could be used in the food, pharmaceutical and optical tech industries. But for now, the glass you encounter every day will definitely have been made with sand.
What else is sand used for?
As well as being integral to the manufacture of glass, sand is used in a surprising number of ways.
It hasn't always been used for good. In classical and medieval times, it was heated up and poured on invading enemies.
More positively, it's a principal component of three other building materials: brick, cob and concrete. It's also mixed with cement and lime to create building mortar.
Ever seen walls, ceilings and floors with an intentionally gritty texture? Chances are that's because they've been painted with a mixture of sand and paint.
So far, so everyday. But did you know that sand has been used to construct artificial reefs and islands too?
There are plenty more uses, but we'll leave you with one that's close to our hearts here at ToughGlaze: sandblasting.
This is when you blast sand at a glass sheet, creating a milky-white effect. You can sandblast the whole sheet for tinted glass or etch logos and other visuals onto the surface with a stencil.
Sandblasting isn't always done with glass – sometimes processors use crushed-up walnut shells instead. But as the name suggests, sand is often the go-to material for the process.
Sandblasted glass is often used for privacy in bathrooms and front doors. But you can also see sandblasted designs in offices and other commercial spaces.
So there you have it: a whistle-stop tour of the essential role played by sand in glass production. We hope it's given you some food for thought.
Are you looking for a trusted glass processor?
Get in touch with ToughGlaze today for a quick, competitive quote.