How do glass suppliers cut glass?
Share this blog:
How do you cut glass without it breaking? Find out the most common methods used in glass manufacturing.
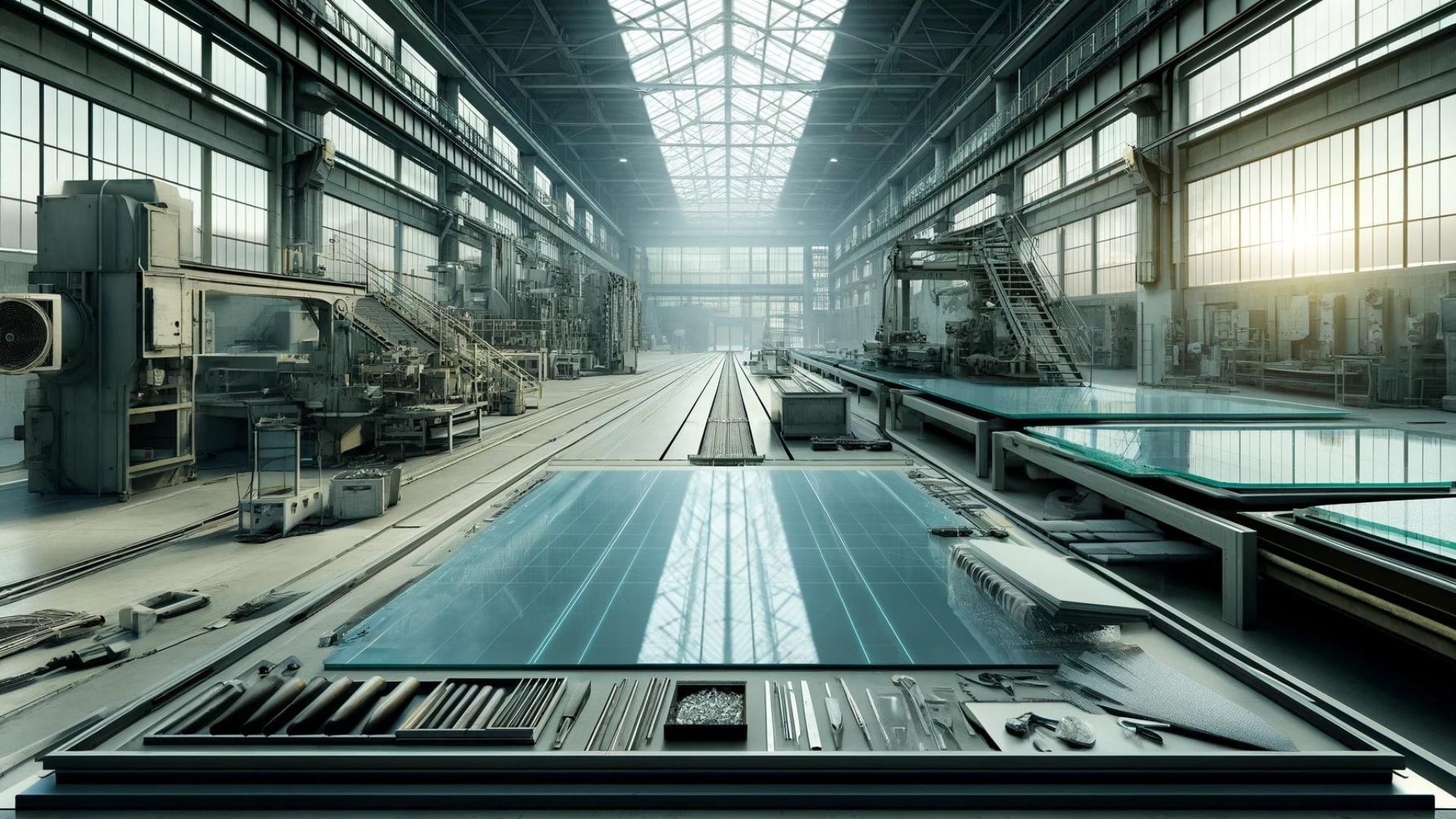
Glass is such a fixture of our everyday lives that it's easy to overlook just how remarkable it is. How can a material made primarily out of sand be used for glass walkways, facades and skyscrapers?
Part of the mystery is down to the fact that glass isn't a material most of us will ever handle or shape. You'd be hard-pressed to go through life without ever sawing, sanding or screwing a piece of wood – but 99.9% of the time, we get our glass ready-made from the manufacturer.
How, for instance, do you cut glass without it shattering? The answer is more complicated than you might think as there's no one method used by all glass manufacturers.
1. Cutting with wheels
Since the 19th century, glass manufacturers have been using wheels to cut glass. But over the years manual wheel cutters have been replaced by cutting machines.
A cutting machine looks a bit like an oversized paper guillotine. The wheel moves over the sheet of glass, creating incisions. Over the years, these wheels have been developed to cut thinner and thinner sheets of glass.
Different machines are built for different purposes. You need a different machine for laminated glass, say, than for traditional float glass.
Some of these cutting tables are CNCs: computer-controlled machines that can be fed designs which they execute with precision.
Wheel cutting, however, has one disadvantage. The resulting glass tends to be chipped, meaning it needs additional processing. However, this isn't a problem if the glass processor has the right tools.
2. Water-jet cutting
Other glass suppliers use water-jet cutting. This is where a jet of highly pressurised water is fired at the glass.
Perhaps the biggest strength of this method is its versatility. Water-jet cutting can be applied to any type and any thickness of glass, including laminated glass. Unlike with wheel-cutting machines, you don't need to have multiple tools for multiple products.
The narrowness of the water jet means that the cuts are smooth and precise with minimal kerfs (those slits and notches that are caused by the cutting process).
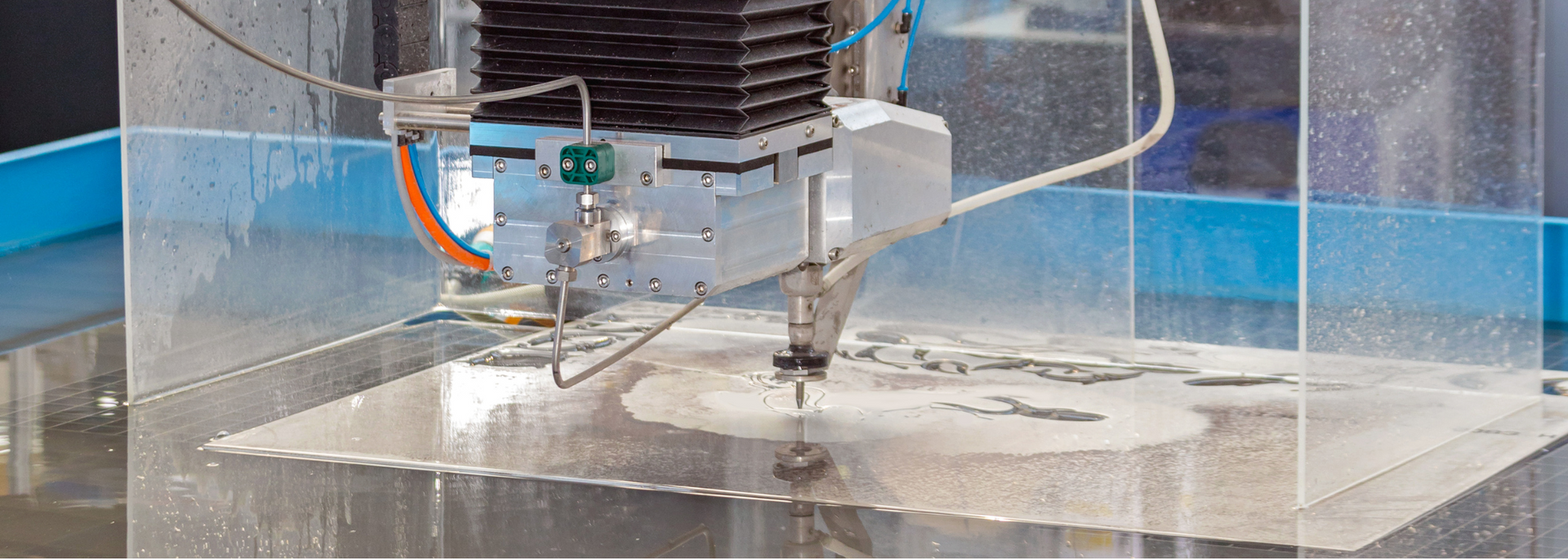
Glass processors also employ a method called "stacking", where multiple panels are placed on top of each other and cut simultaneously with the water jet. You can also use a multi-axis water jet to create complex cuts.
Overall, water-jet cutting is a versatile and cost-effective way to get glass panels ready for market.
3. Cutting with CO₂ lasers
Wheel cutting and water-jet cutting depend on contact with the glass. But laser cutting is contactless, with only heat from a laser beam touching the glass.
This method of "thermal stress cutting", as it's known, involves aiming a laser at a specific line on the glass. This is then followed by a cold jet of air or liquid to cool the glass down.
The heat causes tension in the glass that fissures it. It's a precise, clean method of cutting, producing glass without cracks or chips that doesn't need to be processed, ground or polished.
Its main drawback is that it has only a limited ability to cut geometric shapes. This is where ablation (or laser shape cutting) comes in.
This method works the same as standard laser cutting – but it allows you to cut shapes inside the glass. It can, for instance, be drilled, grooved, marked, patterned and chamfered.
Both methods produce clean glass. Ablation, however, is very much at the pricey end of the spectrum.
6. Filament cutting
Filament cutting was developed at the University of Toronto in the early 2010s. It involves shooting ps-laser pulses at strengthened glass. These pulses are fine enough for free shape cutting.
Once the laser has fractured the surface, the shaped glass has a ground-like surface and a good bend strength. The product is clean, with minimal micro-cracks and no surface marks.
Filament cutting is a relatively recent development, so more research and development is needed before its benefits are fully known.
DIY methods
The above methods are used in commercial glass manufacturing. However, glass also needs to be cut for a variety of craft projects. The most commonly used tool for the job is a glass cutter – but if you don't have one to hand, there are alternatives.
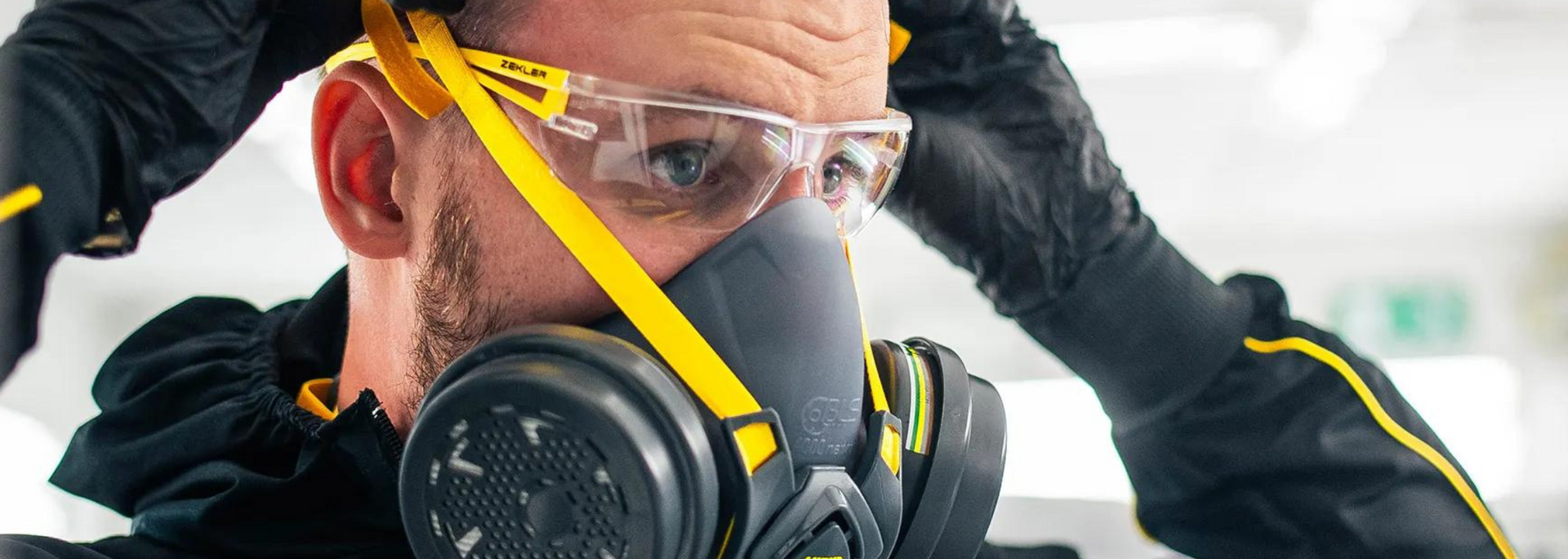
Before we go any further, it's important to say that you should wear protective gloves, eye goggles and a dust mask before attempting to cut glass, no matter how you go about it.
The first method involves lighting a piece of string that's been soaked in rubbing alcohol or acetone and tied around a piece of glass. Once the string is burnt out, you plunge the glass into cold water, where the sudden change in temperature causes it to break.
Then there's using a carbide scribe or large nail to score the glass. You then apply pressure to achieve a clean break.
Finally, you can use a Dremel or rotary tool with a diamond cutting wheel attachment.
How has glass cutting changed over the years?
Back in the Middle Ages, glass cutting was done manually. A rod of iron with a sharp point would be heated in the oven. When red hot, the point would be drawn along the glass until it snapped.
The main problem with this method was that it lacked accuracy. Once snapped, the pieces had to be trimmed to shape: a process known as "grozing".
In the 14th and 16th centuries, Italy was a hotbed of glass production. Manufacturers developed a diamond-tipped cutter which allowed for more accuracy than the mediaeval rod.
Then in 1869, Samuel Monce of Bristol, Connecticut developed the wheel cutter which is still used to this day.
Conclusion
Glass cutting is an essential part of glass manufacturing – but like handwriting and cat skinning, there's no one way to do it. We hope this article has helped you get to grips with some of the most commonly used methods.
Are you looking for high-quality
toughened,
laminated or
decorative glass products? At ToughGlaze, we process and cut all our products at our state-of-the-art UK facility.
Get in touch to request a quick, competitive quote.