What goes into glass? Mapping the glass fabrication value chain
Share this blog:
Around 500,000 Europeans work in the glass industry. What do they do? Learn about the glass value chain.
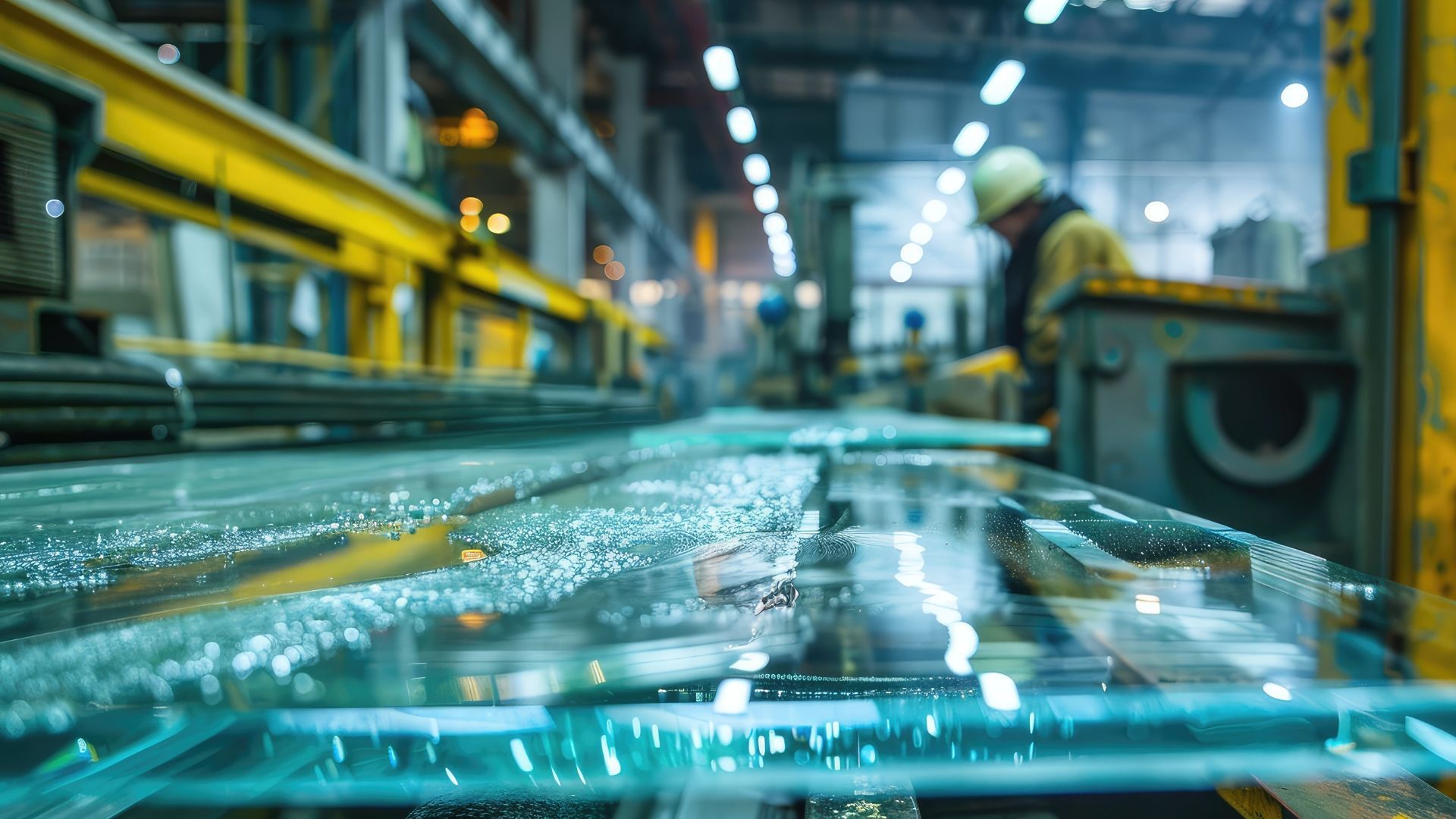
Glass is one of the most commonly used materials in the world. It's integral to everything from domestic windows to commercial skyscrapers. So, how do glass fabricators get it from A to B?
Raw materials have to be sourced. Manufacturers turn it into glass. Processors cut, etch, notch, bevel, colour, toughen, laminate and texture it. Then it gets delivered to the customer.
For this process to be executed, companies must carry out a series of activities known in business management as a "value chain".
A value chain is more than just a manufacturing process or a delivery system. It refers to
all the processes that get a good or service – in this case, glass – to the customer.
The term comes from Michael Porter's 1985 book
Competitive Advantage: Creating and Sustaining Superior Performance.
It's been summarised by the Institute for Manufacturing, Cambridge, as "based on the process view of organisation, the idea of seeing a manufacturing (or service) organisation as a system, made up of subsystems each with inputs, transformation processes and outputs".
This covers everything from money and labour materials to equipment and buildings, from admin to management, from the factory floor to the shop floor.
So, what does this value chain look like in the glass industry? Let's find out.
The picture in Europe
You can get a good sense of the complexity and interrelatedness of glass fabrication by looking at these statistics from
Glass Alliance Europe. The industry, it says, covers 25 European countries, 500 glass manufacturing plants, 500,000 jobs and 40 million tonnes of glass each year.
What do those 500,000 people do? It all begins with the raw materials needed to make glass.
1. Sourcing materials
The main material needed for glass is sand. In fact,
glass can be made from sand alone, as in the case of
naturally occurring glass. But to manufacture glass for commercial use, you need more than just sand.
Glass manufacturers
Pilkington, for instance, make glass with 59% sand. This gets mixed with soda ash, dolomite, limestone, salt cake and cullet.
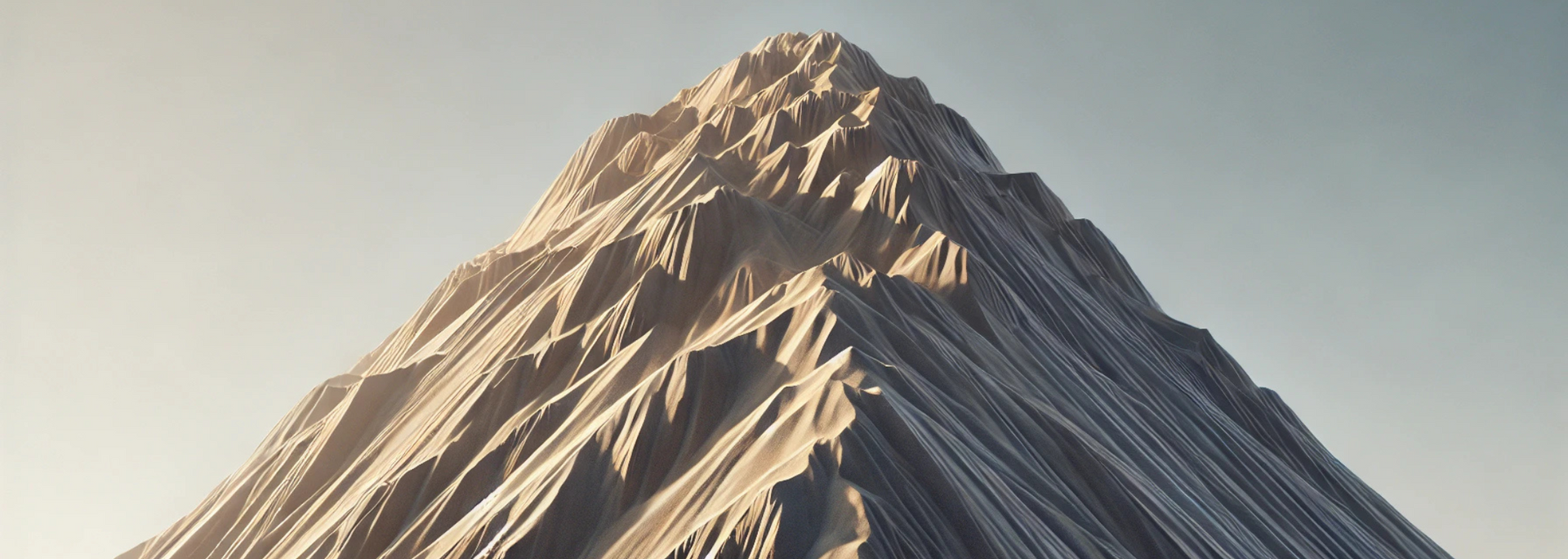
All these materials need to be quarried and transported – except for cullet. This is waste glass that gets recycled in the manufacture of new glass products.
Most cullet used to manufacture float glass is "internal" – in other words, it consists of cast-offs from the manufacturing process. At the time of writing, only a tiny amount of cullet comes from consumers.
2. Making glass
Once the materials have been sourced and transported, it's time to make glass. The ingredients are mixed and melted at a white heat until the mixture becomes viscous. When it sets, you've got glass.
Of course, not all glass manufacturing processes are the same. Take
toughened glass, our speciality. Toughened glass is fired at a high temperature and then quickly cooled or "quenched". This changes its chemical composition, making it harder to break than standard float glass.
When toughened glass breaks, it breaks into lots of tiny, relatively harmless pieces. This means it must be cut to size
before going into the furnace. Try to cut it afterwards and you're looking at a broken pane of glass. (Cue sad trumpet sound.)
3. Glass processing
The glass is out of the oven. It can now be decorated in myriad ways.
Glass processing is a kind of alchemy. It turns plain old panes of glass into
colourful,
textured,
printed and even
dimmable materials that can be used in a huge range of settings.
We don't have space to go through all the different ways you can process glass. But one clear indication of the versatility of glass is the multitude of ways you can add designs to it.
You can
sandblast glass, creating a frosted effect or a stencilled-off textured design. You can
digitally print glass with photorealistic images. You can add a
coloured or
textured interlayer.
You can also make
switchable glass. This lets you change its transparency levels using smart technology. Want some privacy? Simply press a button and the glass turns opaque.
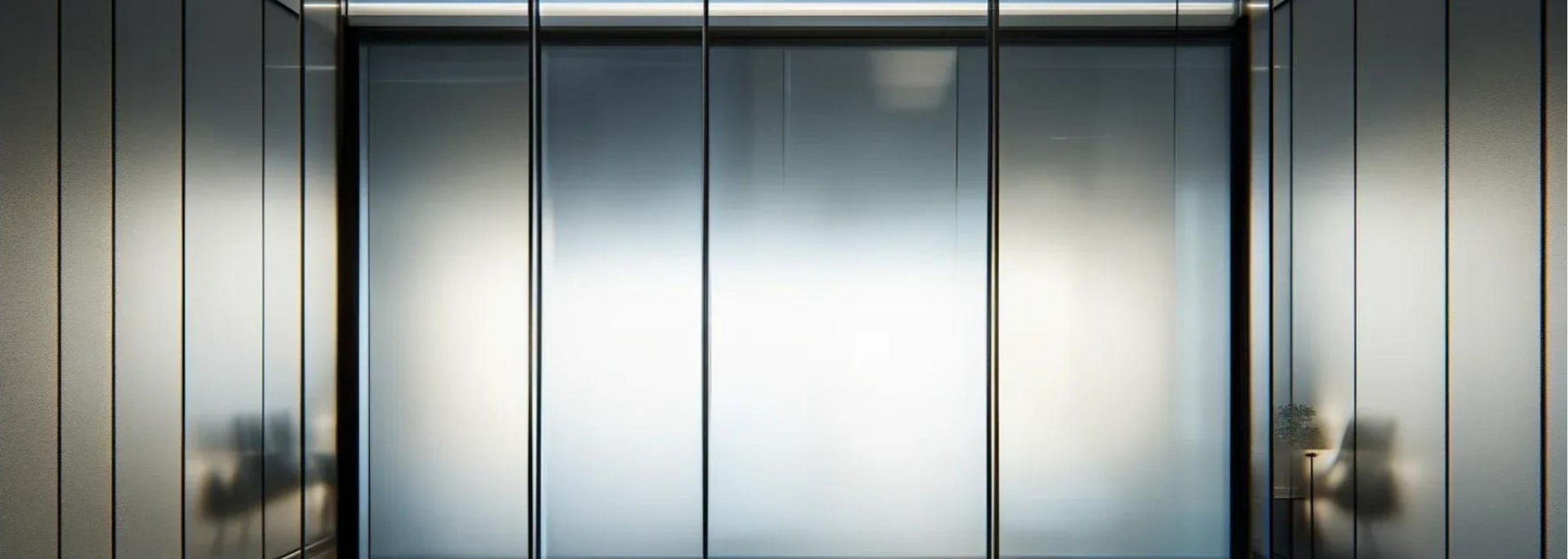
Sometimes, glass manufacturers also process glass. In other cases, glass processors acquire raw glass sheets from suppliers and then process them on-site.
4. Delivery
The last link in the value chain is delivery. Glass travels all over the world to reach clients – and because of glass's fragility (relative to materials like steel and concrete, say), it needs to be handled with care.
Some manufacturers and processors outsource delivery to another firm. Others have their own in-house fleet. At ToughGlaze, for instance, we have more than 30 vehicles delivering our glass products across the UK mainland and beyond.
When ordering glass, you should always look for industry accreditations. In the case of glass delivery, look out for the Fleet Operator Recognition Scheme (FORS). This can help reassure you that your order is in safe hands.
About us
At ToughGlaze, we believe that product quality and customer satisfaction are two sides of the same coin. That's why we make, process and deliver our glass products all from under one roof, right here at our state-of-the-art facilities.
This means one thing for you: peace of mind. If you're sourcing glass from one supplier, getting it processed by another and then delivered by another, you're creating a chain of possible delays and disruptions.
After all, if you receive substandard materials or even good-quality materials too late, it's you who has the explaining to do. By working with a company like ours that does everything from one place, you significantly reduce the chances of this happening.
Our range covers everything from functional
toughened and
laminated glass to
decorative glass and
structural glazing. It's tough, long-lasting, aesthetically pleasing, thermally efficient and cost-effective. Oh, and all our products are in line with BS EN standards and have received the Kitemark seal of approval.
So, if you're in the market for some high-quality glass,
get in touch with us today for a quick, competitive quote. We'd love to set you up with the right materials for the job.