Solutions for reducing water waste in glass processing
Share this blog:
Glass fabrication and processing uses lots of H₂O. How is the industry reducing water waste? Let's find out.

The glass industry, like many others, is united in its efforts to become more sustainable.
And in some ways, it has a head start. Glass, you see, is an infinitely recyclable material. If you melt glass and reform it, you get new glass. Glass that's as strong, clear and versatile as it's always been – and always will be.
The same can't be said for industries that deal with plastic, say, or paper. These materials degrade with each round of recycling. Plastic can typically only be recycled two or three times before the quality becomes too poor to use again.
So, glass manufacturers and glass processors have a material advantage – literally. But while they might have a head start in the race to a circular economy, they still have a few hurdles to leap along the way.
Chief among these, perhaps, is that glass processing demands colossal amounts of resources. A glass toughening furnace is basically a huge electric oven – and unlike your Electrolux, it has to reach temperatures of 650ºC (1,202ºF) or more. That means more amps than a Metallica concert.
And then there's water. Glass processors use gallons upon gallons of water. The glass that leaves that toughening furnace needs cooling – most likely using water. And all the cutting and grinding machines that cut and grind all day long? They need water, too. And the water that runs off these machines is contaminated with glass particles, which you certainly don't want to end up in your morning coffee.
So, when it comes to the wet stuff, glass companies have two problems to solve. The first is resource management: they use lots and lots of water and this is bad for the environment and their bottom line. The second is contamination, which introduces its own raft of problems relating to wastewater management and compliance.
How does the glass industry manage this? Let's find out.
Closed-water process systems
Using a closed-water system is like maintaining your own miniature (or not-so-miniature) water supply. The water you use to cool and grind your glass is pumped into pipes, where it's filtered, treated and stored in tanks, ready to use again.
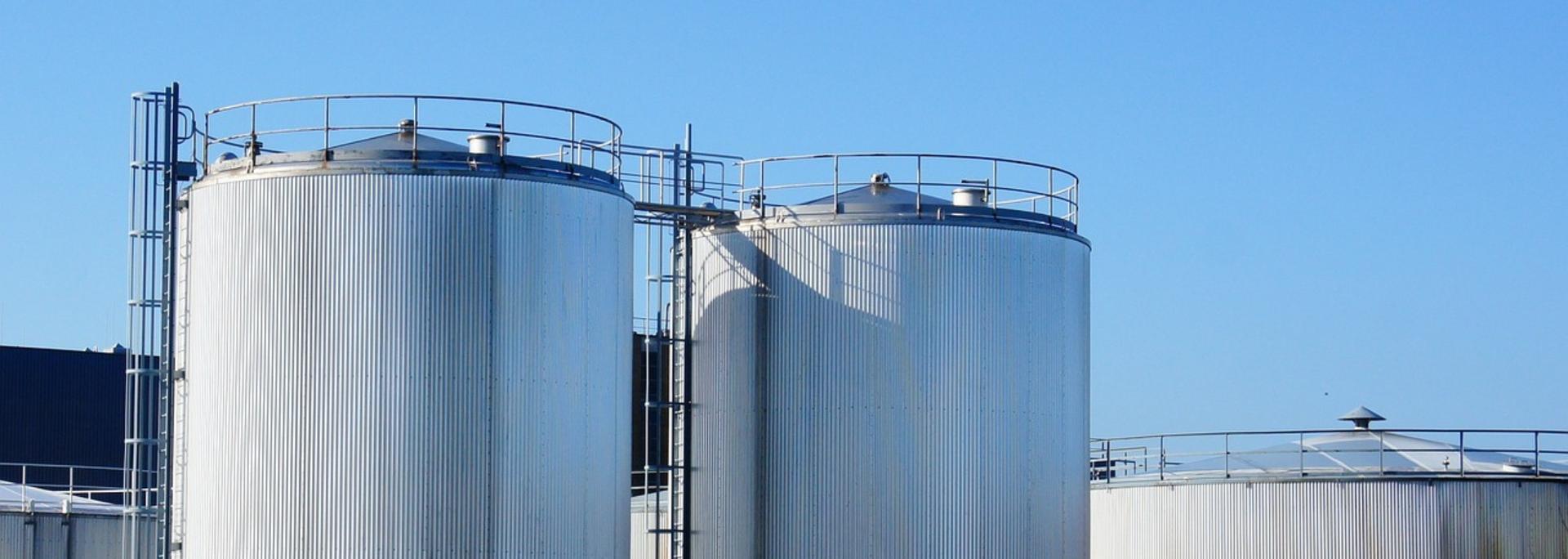
You'll never quite be able to reuse all your water. You'll still need top-ups from the main supply – and some waste from leaks and evaporation is inevitable. However, the positive impacts on the environment and operational efficiency are significant. One treatment company claims that a recycling solution like this "can reduce water consumption from the grid by up to 85%".
And closed-water systems have benefits beyond reducing water waste. For instance, many glass processors add liquid coolants to their water. Reusing the same water means you'll use less coolant because it only needs to be added once.
Sludge treatment
Yes, "sludge" is a technical term. It refers to the thick, mulchy stuff that accumulates in wastewater. In glass processing, this stuff will typically be tiny glass particles called "finings", along with oil and other liquid and solid contaminants.
There are limits on how much of this stuff can go down the drain – and these limits are defined by government regulations, community demands and an organisation's own environmental policy.
Moreover, contaminated water can't be pumped back into the factory without being cleaned first.
To address these issues, glass fabricators and processors typically employ sludge treatment systems as part of their wider closed-water systems. This involves several processes, including sedimentation and filtration.
Sedimentation deals with larger particles. The water sits in vats and the particles simply float to the bottom, where they can be collected. A polymer flocculant can be added to accelerate this process.
Filtration, meanwhile, catches the smaller particles, which remain suspended in the water even after sedimentation has occurred.
After filtration and sedimentation, you're left with two byproducts: clean, reusable water and lumps of brittle, fibrous matter that can be disposed of with general waste.
Reuse clean-in-place systems
A clean-in-place (CIP) system involves pumping water through machinery to clean it. This allows for regular, automated cleaning without dismantling the equipment.
CIP systems have been around for many decades – since the 1950s, in fact. But like other industrial processes, they've received scrutiny for their environmental impact. CIP helps to improve production efficiency by reducing downtime – but is it as much a boon for resource conservation?
One way to reduce water consumption is to employ a reuse clean-in-place system. This operates much like the closed water system discussed earlier – but on a smaller scale. After the first flush, water is collected and circulated through the system for the second flush.
Water on demand
Think back to your childhood. Did your parents or caregivers ever tell you off for leaving the tap running while brushing your teeth?
That's what we mean by "water on demand". It's the principle that you should only use water as and when you need it. Finished grinding that glass? Time to turn off the water supply – automatically, if possible.
It's as simple as that. If a child brushes their teeth with the tap running, they waste water. If a glass treatment plant runs a water jet-cutting machine without turning off the supply between cuts, it wastes water.
The difference, of course, is scale. That child might waste four gallons every time they forget the faucet. But in an industrial setting, you can expect to waste much, much more than that.
How ToughGlaze reduces water waste
Here at ToughGlaze, our environmental responsibility and operational efficiency are both high on the agenda.
That's why we're always developing new ways to reduce waste, cut overheads and provide the best possible service to our customers.
In fact, our co-founder, Ashok Varsani, developed his own system to filter and recycle water used for our cutting, grinding and cooling processes.
But sustainability is a journey – and like most companies, we're not quite there yet. However, with our track record of innovation, you can bet we'll be one of the first over the finish line.
Founded in 1993, ToughGlaze has fostered a reputation for delivering quality and value in the UK glass industry. Learn more about our state-of-the-art
glass toughening plant and our long and proud history. Or
get in touch with our experts for a quick, competitive quote.