How to order glass: the process from A to Z
Share this blog:
Looking to order some glass? Follow our guide to make sure you get the right materials for the job.

Are you looking to order glass for a construction, glazing or shop-fitting project? Whether it's a single window or a multi-layered structure, you need to be sure you're getting the right materials for the job.
Compared to players in other industries, however, glass manufacturers, processors and suppliers need lots of information from you. Without the right information, you're likely to end up with the wrong materials – meaning either a botched job or a time-consuming replacement process.
When ordering glass, then, it's important to do your homework to give yourself the best chance of success.
At ToughGlaze, we believe an informed customer is a happy customer. We see our job as entering into a relationship with each client – a relationship where effective communication is key.
Because of this, we've put together a handy guide to ordering glass. Follow these five steps and you'll be thanking us later!
1. Know what you need
Sounds obvious, right? But, in fact, getting the right glass for any job is harder than you might think.
This is the direct result of a positive trend in the glass industry: the movement towards ever-greater choice.
It's never been a better time to buy glass. You can get glass that's
toughened or
laminated for extra safety. You can get glass that's been
fire-rated for extra heat protection. Glass that's been
soundproofed. Glass that's
built to withstand bomb blasts. Tinted. Frosted.
Sandblasted.
Screen-printed… Have we made our point yet?
This means you can get glass that's got just the right strength, thickness, durability and appearance for your project. But research is essential to find out what it is.
2. Know your measurements
Again, this might sound obvious. But it's important that, as a customer, you tell us exactly how big your glass should be.
This isn't a case of pedantry, either. We're here to provide materials, not tell people what they need. But in the world of glass, measurements are crucial to the safety of an installation. Get them wrong and you could end up with materials that are not quite strong enough or don't quite fit snugly.
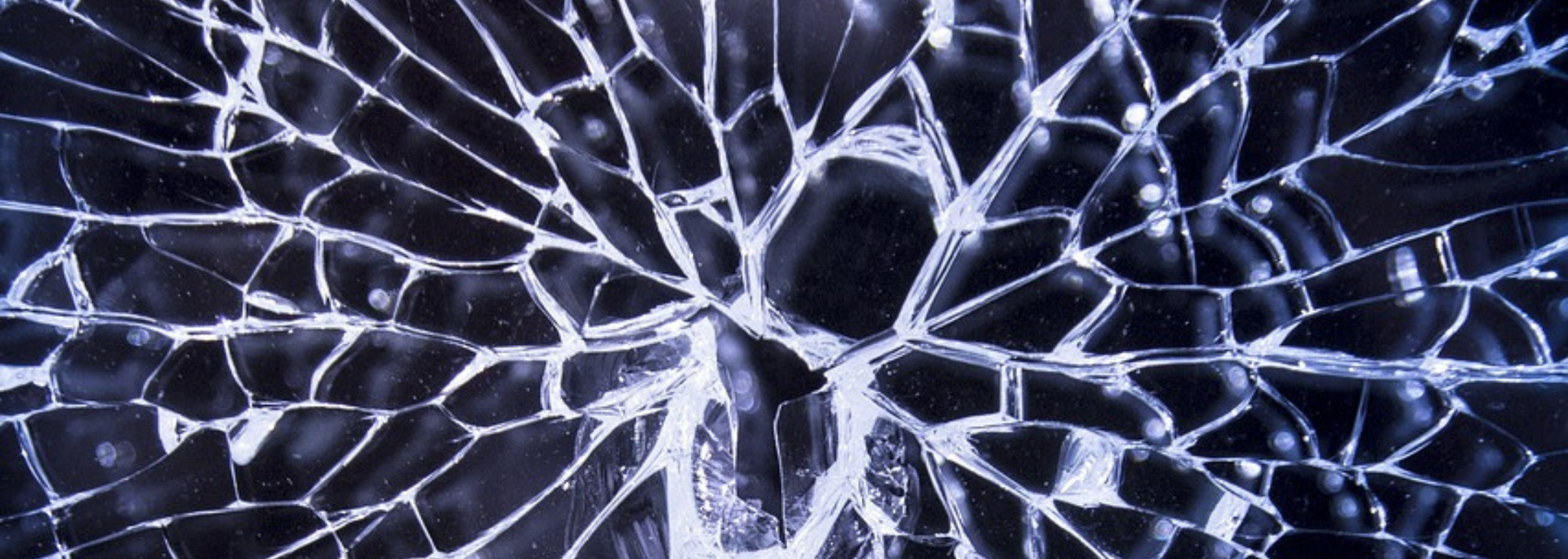
You could say it's like shopping for clothes – but a baggy waist or tight collar isn't a matter of life and death.
So, before you get in touch with a processor or supplier about the glass you need, make sure you've checked and double-checked your measurements. After all, they can only give you what you ask for.
3. Know your tolerances
Tolerances are an essential but often misunderstood aspect of glazing.
Perhaps it's the word itself that's the problem. The concept becomes altogether easier to grasp when you replace the word "tolerance" with the phrase "wiggle room".
Every piece of glass needs to be the right dimensions. But often, you can get away with a millimetre here or a millimetre there. These minimum and maximum variations are your tolerances – and they're essential information to include when you're ordering glass.
It's also important to note that tolerances are the buyer's responsibility. If you don't communicate your requirements effectively, it's on you to pay for replacement panels – not the processor.
So whether you're fitting a single splashback, multiple partitions or anything in between, know your wiggle room. It's vital to the success or failure of any glazing project.
4. Know your turnaround
Any installer or architect will tell you that the success of a project doesn't just depend on the materials – it also depends on a well-oiled schedule.
When ordering glass, make sure you've left enough time for the glass to be cut, treated and delivered. Otherwise, you're looking at delays (also known in the business as "a waste of money").
You should also factor in delays on the supplier's side. Of course, a reputable firm will always process their products on time. But sometimes, delays are out of their control – especially at a time when supply chain disruptions are the rule rather than the exception.
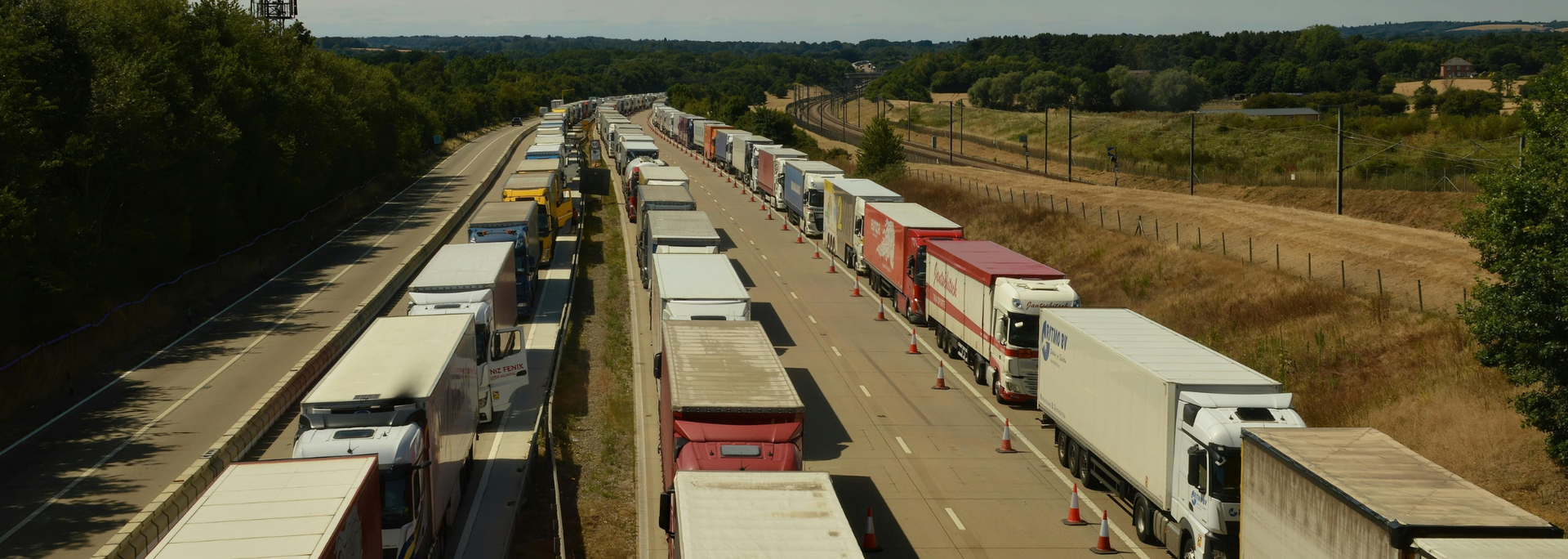
Before you place an order for glass, make sure you know when you need it and what will happen if there are unavoidable delays. Communicating this to your glass processor increases your chances of success.
5. Know what to look for in a provider
In some ways, this is the most important point of all. You can pick the best product in the world. You can make sure your measurements and tolerances are bang on. You can plan your project with military precision.
Sadly, none of this will add up to a hill of beans if you work with a bad provider.
Picking the right provider isn't easy in a crowded market. But at the very least, you need to be sure they're experienced and accredited.
Look for accreditations such as ISO standards and Kitemark approval. These are objective standards that demonstrate excellence. Without them, you're pretty much shooting in the dark.
If you're ordering toughened glass, you might also want to check if your provider offers
heat soak testing. This can dramatically reduce the possibility of spontaneous breakage.
Ultimately, a good provider can make the difference between a successful job and a logistical nightmare. Don't cut corners – shop around and pick the right provider for you!
Bonus tip
Follow these five steps and you're in with a shot of getting the right materials for your project. But here's a bonus tip for you: at every step of the process,
ask questions.
Yes, it's a simple piece of advice but so often neglected. If you're unsure about something, ask! Treat your provider as a partner – one who takes the success of your project as seriously as you.
At ToughGlaze, we treat our customers as partners. Any questions?
Just ask.
Are you looking for high-quality,
made-to-measure toughened glass? Don't hesitate to
contact ToughGlaze for a quick, competitive quote.