How is laminated glass made?
Share this blog:
Laminated glass is used wherever extra safety is required. But how is it made? Find out in our guide.
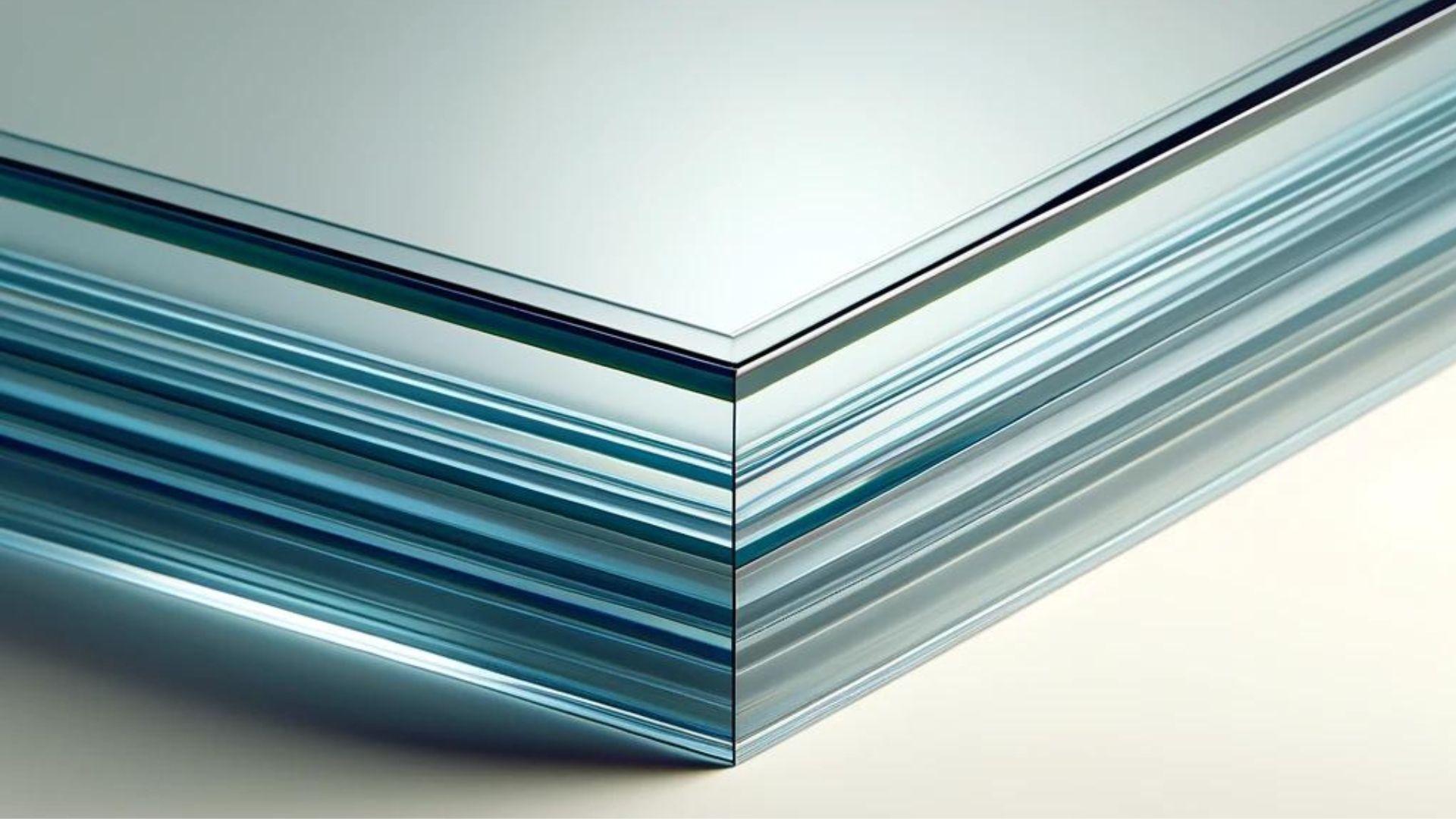
A world without laminated glass would be a riskier place. Why? Because this essential material is manufactured in such a way that it never shatters into pieces. Instead, it retains its structural stability.
Think of an action movie. Tyres explode, cars go up in flames – but the windscreen always stays intact, no matter how cracked it gets. That's all thanks to laminated glass.
And it's not just used for windscreens. Laminated glass is also a staple material for storefronts, doors and structural glazing – pretty much any location where safety glass is recommended or required.
But why does it break like that? It's all about the manufacturing process.
The basics of laminated glass
Laminated glass is a kind of glass sandwich. You take two glass panes – often toughened – and put a vinyl layer in between.
This vinyl layer is the butter to the glass panes' bread. But it's a strong, gluey butter that bonds the surfaces together and prevents them from breaking into large pieces.
What's the process?
The exact process will differ from place to place. But typically, the manufacturing process for laminated glass looks something like this.
First, the glass panes are cut to size with a CNC machine. This is a computer-controlled machine that's kind of like a paper guillotine, only bigger and more powerful.
Next, it's polished and washed by hand. Blemishes are removed so the glass looks good before the toughening process begins.
Next up is the toughening itself. The panes are fed into a furnace and rapidly cooled to room temperature. This process excites the molecules in such a way that the panes break into small pieces rather than hefty shards.
Fresh from the furnace, the panes of glass are cleaned again.
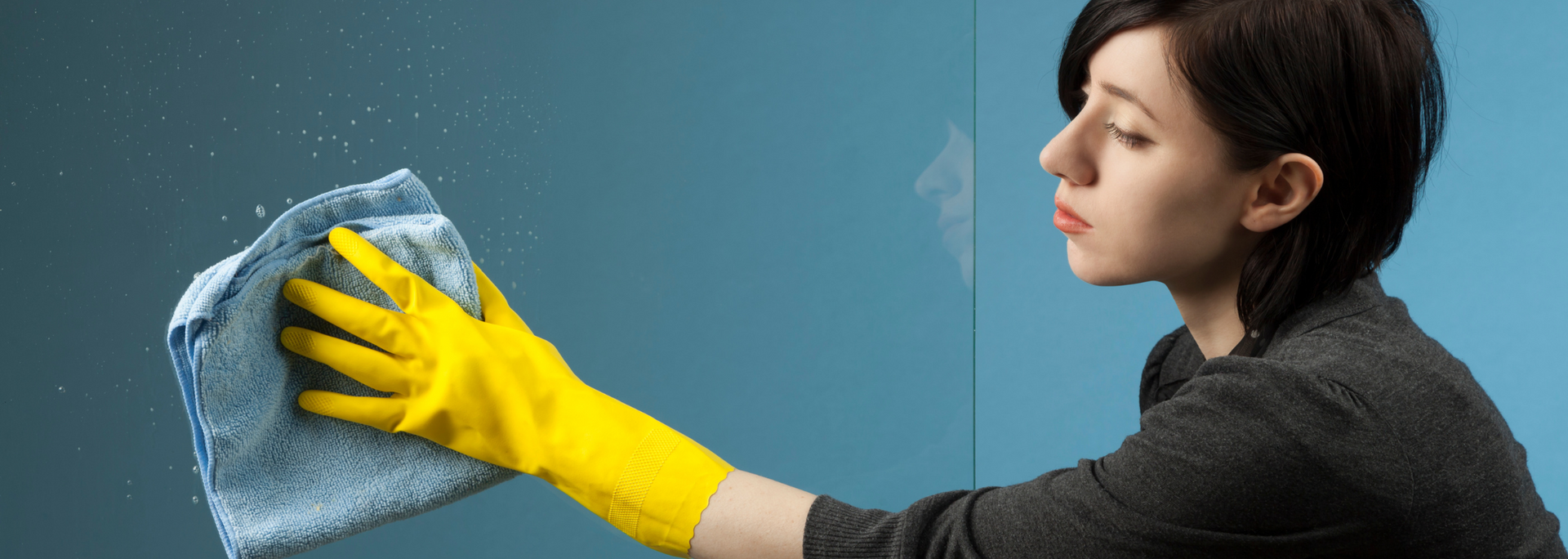
Once the panes are sparkling, the manufacturer moves on to the interlayers. There are three main types of interlayers: PVB, EVA and SGP. We've gone into detail about the differences between laminated glass interlayers before.
The interlayer is as vital to the finished product as the filling is to your favourite sandwich. Without it, the glass won't have its characteristic properties.
Laminate interlayers are cut and applied to the first sheet of newly toughened glass. At first, it looks like a baggy tablecloth until the interlayer is trimmed to fit the glass. The sandwich is now taped into place ahead of the laminating process.
The glass then gets sealed inside a hot silicone bag that acts as a protective layer. It's placed in the oven and the lamination begins.
This heating cycle permanently bonds the layers together. It's this part of the process that makes laminated glass the ideal choice for applications where safety glass is required.
The length of the heating cycle depends on the thickness of the glass. Usually, it takes around three or four hours.
Once laminated, the glass is left to cool. When it's safe to do so, the tape is removed and the glass is good to go.
A brief history of laminated glass
Laminated glass is one of those products which might never have been invented if it wasn't for a happy accident.
Edouard Benedictus was a French scientist, composer, writer and painter. Despite these many talents, he wasn't above making a mistake.
One day in 1903, he was climbing a ladder in his chemistry lab and accidentally knocked a glass flask over. It fell to the ground and shattered – at least that's what Benedictus thought.
On closer inspection, he saw that the flask had shattered but still kept its form. The glass had broken into shards – but these had stayed together in a kind of transparent spider web.
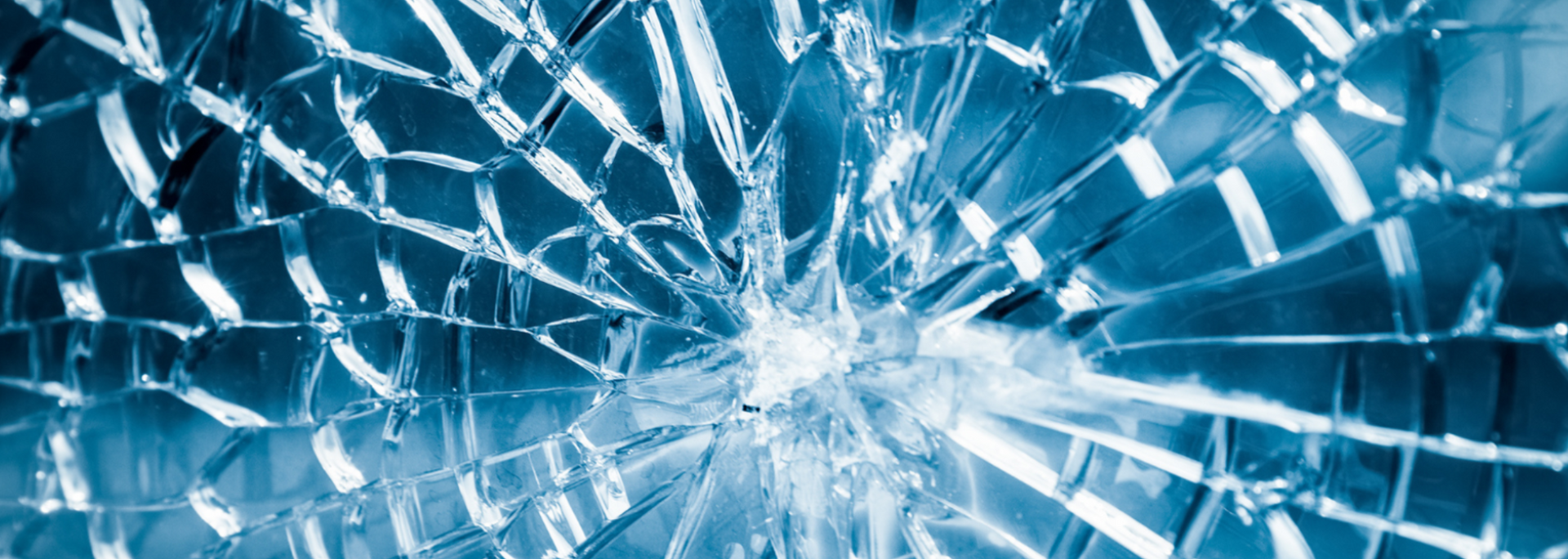
Being a scientist, Benedictus couldn't let this pass. He wanted to know why the flask had broken in this unusual way.
His assistant told him that the flask had previously been full of cellulose nitrate. This liquid had evaporated but left a thin, transparent coating. It was this remnant that held the pieces of glass together.
He might have thought no more of it were it not for another kind of accident – a rise in car accidents taking place in Paris at the time.
Laminated glass and car safety
Benedictus was aware that the current craze for cars on the streets of Paris came with a risk. If an accident happened, the windscreen could shatter into shards that could cause injuries – even fatalities.
He realised that his discovery could be used to make cars safer. If cellulose nitrate could create a shatterproof flask, why couldn't he invent a shatterproof windscreen?
Through trial and error, he found that the best way to do this was by sandwiching a plastic interlayer between two sheets of glass – pretty much the formula we use today.
However, it didn't catch on immediately. Like many new inventions, it was too expensive to produce at scale. However, his Triplex glass was used for gas mask lenses in World War I.
Later developments
In 1905, an English solicitor named John Crewe Wood patented a type of laminated glass to be used in windscreens.
Twenty years later, two Canadian chemists invented PVB – the plastic interlayer that's used in the production of laminated glass to this day. Laminated glass that used this interlayer quickly superseded other kinds on the market.
Today, the formula is pretty much the same – but it's more robust than ever.
Can you cut laminated glass?
The point of laminated glass is that it's extremely hard to break. The plastic interlayer makes it hard to cut – but it is possible to achieve so long as toughened glass isn't involved.
Safe methods include specially built cutting tables, blowlamps, high-pressure water jets and vertical saw frames.
Once the panel is cut, the interlayer has to be separated. Often, it's melted with a heat gun and then cut with a blade.
But remember that toughened glass can
never
be cut. Doing so would cause it to shatter into tiny pieces. That's why laminated glass can only be cut if standard annealed glass interlayers are used.
At ToughGlaze, we provide high-quality,
custom-cut laminated glass to meet your requirements.
Get in touch today for a competitive quote.